Zang’s workshop
The history of the
Zang’s Harvestbooster:
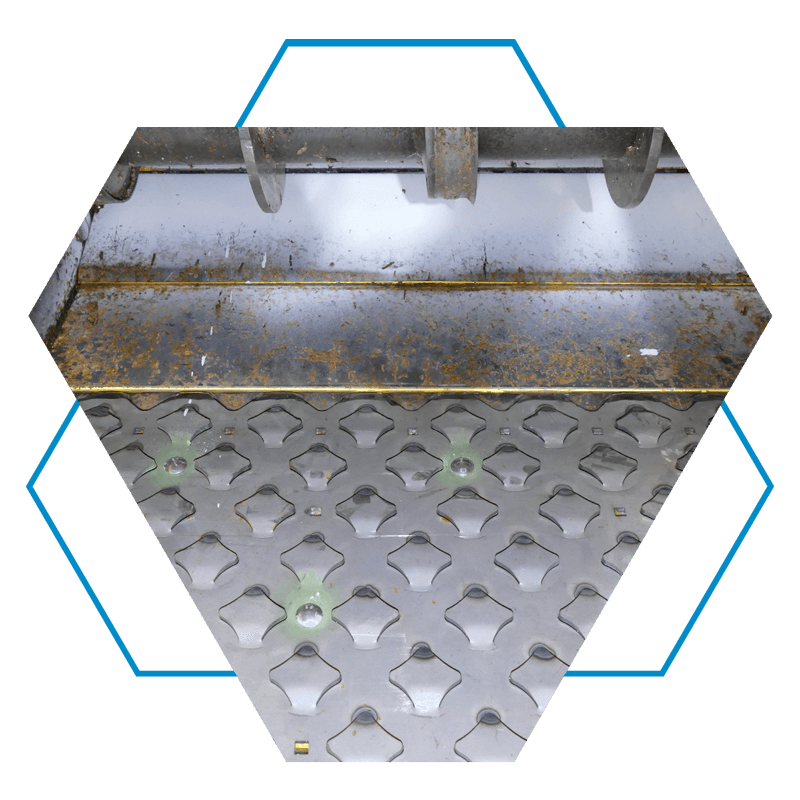
From problem to idea …
Due to inadequate feeding to the threshing organs and poor deawning of the winter barley, we looked for improvement.
Many years of experience in combine threshing combined with our technical capabilities were prerequisites for the development of the parts in the feed and threshing area of our machine.
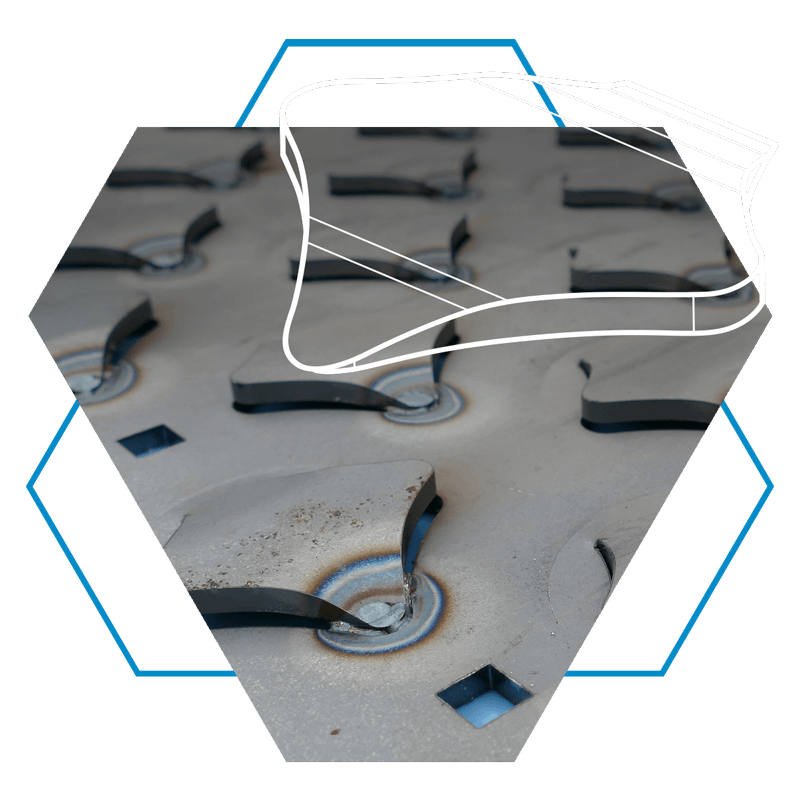
… from the idea
to the construction …
Together with my son Michael Zang, who has CAD experience, we designed an ear release plate in winter 2019. We were looking for a new format of effective elements for such a plate. We cut and forged the first small elements on the plasma cutting machine that my junior built himself.
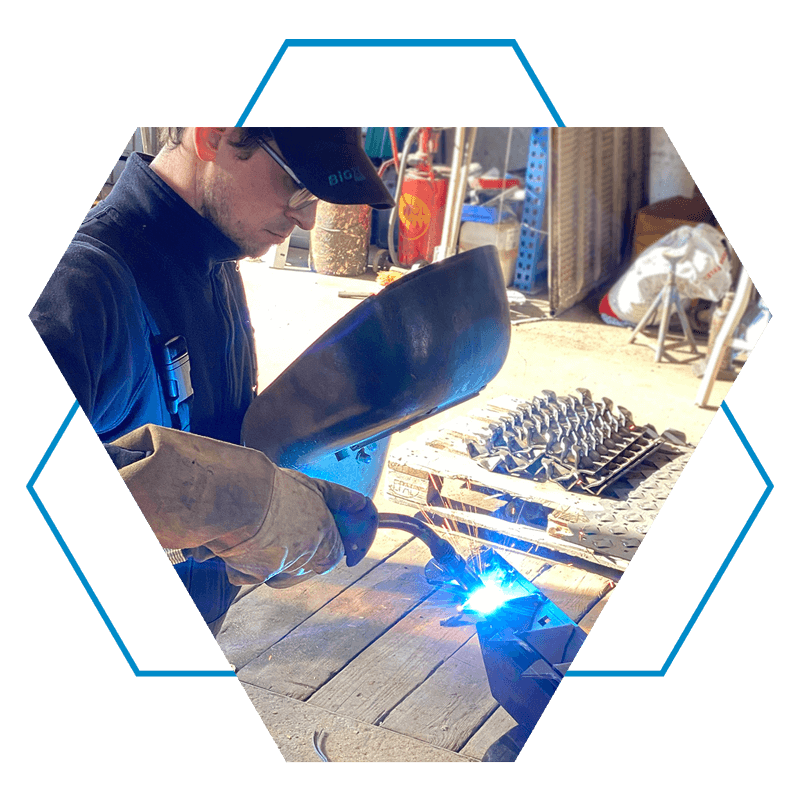
… from the desk
to the workshop …
After production, I shaped each individual element by hand and with a hammer so that it met our ideas and requirements. Now that the shape and dimensions are clear, we have the parts prefabricated. We also built the tool for the 100-ton press, with which the rhombuses are formed, ourselves.
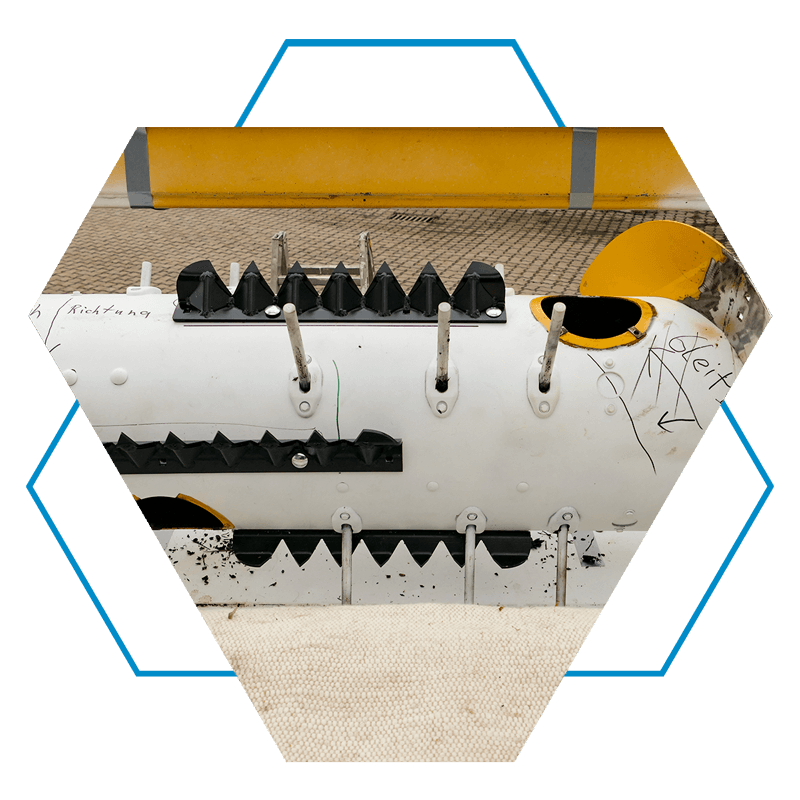
… out of the assembly hall
into the field …
To gain experience, we naturally installed the parts on our own threshers and tested them during grain harvesting. In the first year, we built a total of two ear opening plates, but only one complete kit was installed in our CR 8080 combine harvester. Obviously we had done a lot of things right from the start, which is why we were able to achieve very good results straight away. You can read more about this in our 2020 duck report.
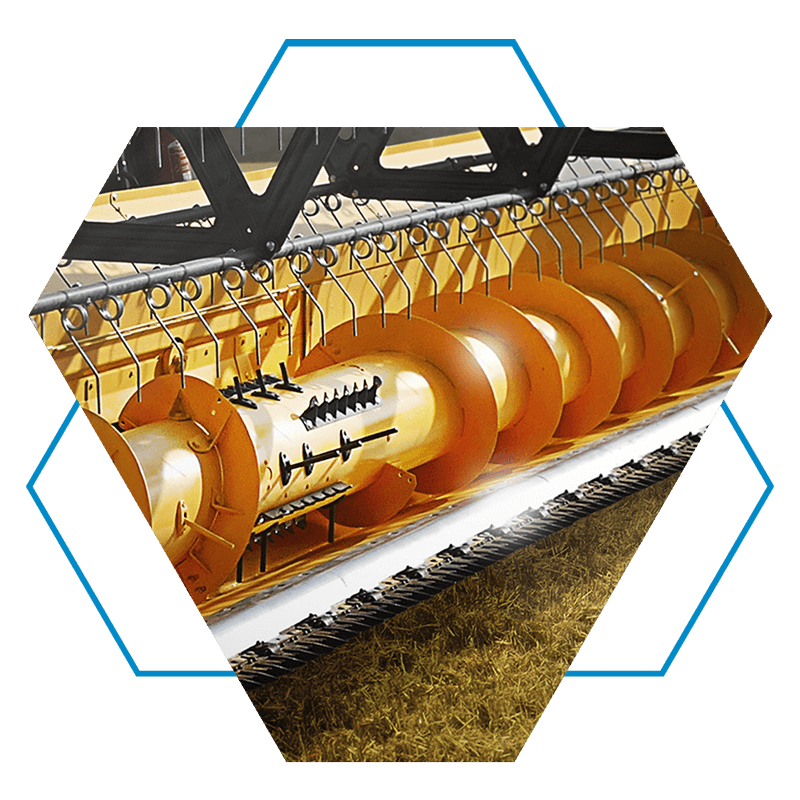
… from Schöllkrippen
to the whole world!
After we had successfully tested our product, I also informed AB of our experiences. Convinced by our work and our development, there was a lot of interest and we set up a joint sales organization. In our first season together, we were able to sell around 100 booster packs and bring them to harvest.
We incorporate our experience into the process of further development.
During the development of the ear lifting plate and after several test variants, we arrived at the shape of a rhombus with concave flanks and lowered tip that is still used today. This shape guarantees a very good crop flow with equally good effectiveness in terms of
Equalization of the mat and loosening of the grains from the ear.
In order to pull the threshing material safely and without delay over the ear plate, the additional gripper bars were created next. These are welded to the second leg of the feed bars of the conveyor chain in the middle area between the fastenings.
I knew the slide-in bars in a very simple version from the Deutz Fahr combine harvester that I used 20 years ago. Their effect was already good back then, but the side effects were considerable. So the first version was created in 2020 with the double kink and the two approx. 1 meter long parts for each machine. The extreme harvest in 2021 showed us that it works even better with 4 short strips and fewer teeth that are cut deeper. The blunt 45-degree angle of the points is partly responsible for ensuring that no material is carried around or starts to wrap.
Send request
Give us a call or simply send us an inquiry by e-mail so that we can respond to your specific
questions and you can find out more about prices and processing.
+49 (0) 170-8909243